Interview zum FQS-Forschungsprojekt IDaP+: Prozessketten für die Herstellung und Bearbeitung von Gussbauteilen in der Automobilindustrie effizient gestalten und steuern

Die Herstellung von Leichtmetallgussprodukten, gefolgt von Wärmebehandlung und Bearbeitung, ist besonders für die Produktion von elektrischen Antrieben in der Automobilindustrie sowie in anderen Branchen von Bedeutung. Verschiedene Zulieferer, insbesondere kleine und mittlere Unternehmen (KMU), sind an diesen Prozessketten beteiligt. Dazu gehören die Herstellung von Gussformen, das Durchführen von Gießprozessen, die Wärmebehandlung der Rohteile, die Durchführung von Bearbeitungsprozessen als Auftragsfertiger sowie die Bereitstellung von Werkzeugen, Maschinen, Ausrüstung, Software und Dienstleistungen. Aktuell erzeugen all diese Prozesskettenteilnehmer Informationen, die für die Gesamtprozesskette relevant sein können, um einzelne Prozessschritte gezielter einzustellen.
Das über die FQS – Forschungsgemeinschaft Qualität und ASMET – Austrian Society for Metallurgy and Metals geförderte Forschungsprojekt „Integrated Data-based Process Chain Optimisation in Casting and Machining Production (IDaP+)“ untersucht das Potenzial einer durchgängigen Prozesskette und digitalen Vernetzung der betrachteten Bereiche. Durchführende Forschungseinrichtungen sind das utg der TU München (Gießen), das WWWT der TU Wien (Wärmebehandlung und Oberflächentechnik), das ISF der TU Dortmund (Tiefbohren und Gewinden), das IFT der TU Wien (Statorbohren mit sensorischer Spanntechnik) und das IfW der Universität Stuttgart (Statorbohren mit sensorischem Werkzeug). Rund 40 Unternehmen aus Deutschland und Österreich begleiten die Forschungsarbeiten als Industriepartner im Projektbegleitenden Ausschuss.
Im Interview gibt Tim Reeber, Mitarbeiter der Gruppe Prozessüberwachung und -regelung am IfW der Universität Stuttgart, einen Ausblick auf die Projektdurchführung und erklärt, was das Projekt so einzigartig macht.
Aus welcher Problemstellung heraus ist das Forschungsprojekt entstanden?
Tim Reeber: Die Abstimmung der einzelnen Arbeitsschritte bei der Herstellung von E-Mobility – Bauteilen ist derzeit praktisch nicht vorhanden. Dadurch gehen Potenziale in einer aufeinander abgestimmten Prozesskette verloren. Ein Beispiel: Stellen Sie sich vor, ein besonders dünnwandiges Bauteil wird gegossen, dann wärmebehandelt und spanend bearbeitet. Aufgrund des Gießprozesses und der Wärmebehandlung werden im Bauteil mechanische Eigenschaften wie zum Beispiel Eigenspannungen eingebracht. Diese können bei der Zerspanung freigesetzt werden, was sich in Verzug nach dem Ausspannen äußert. Sie können demnach die gesetzten Toleranzen nicht mehr erreichen und ein großer Teil der Wertschöpfung geht hiermit verloren.
Welches Know-how soll im Rahmen des Forschungsprojekts IDaP+ entstehen und wie kann es zur Lösung der geschilderten Problemstellung beitragen?
Tim Reeber: Im Projekt haben wir Experten aus allen Teilschritten sowie die Unterstützung eines breiten Projektausschusses aus der Industrie. Das Ziel ist, die Abhängigkeiten der sequenziellen Arbeitsschritte untereinander und Abstimmungspotenziale zu identifizieren. Dazu werden wir beispielsweise die noch getrennten Simulationsumgebungen aufeinander abstimmen, um aus den simulierten mechanischen Eigenschaften aus dem Guss- und der Wärmebehandlung eine Simulation des Zerspanungsprozesses durchzuführen. Damit sollen schon vor dem ersten Guss eines Bauteils Empfehlungen abgeleitet werden. Auch die im Prozess messbaren Prozessgrößen sowie deren digitalen Austauschmöglichkeiten werden betrachtet. Wenn wir diese Abhängigkeiten verstehen, können Empfehlungen an die Prozessführung bei Guss und Wärmebehandlung abgegeben werden. Aber auch die einzelnen Prozessschritte werden anhand unseres anspruchsvollen Analogiebauteils – ein Statorgehäuse für elektrische KfZ-Motoren – optimiert.
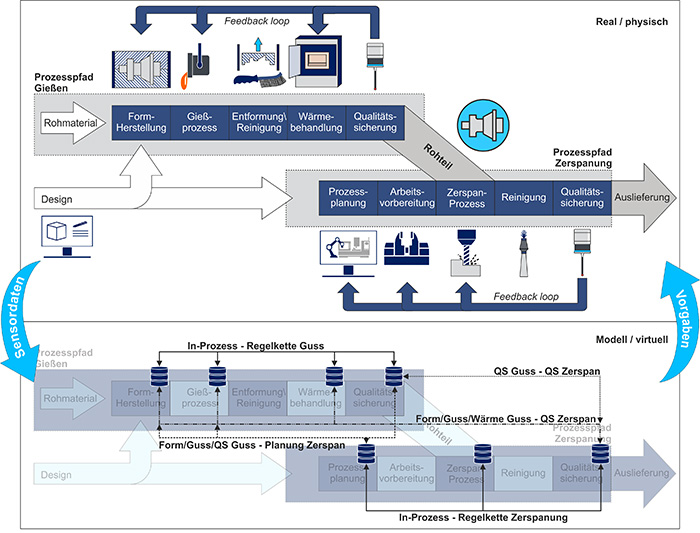
Abb. 1: Zielstellung Forschungsprojekt IDaP+ (Quelle: IfW der Universität Stuttgart)
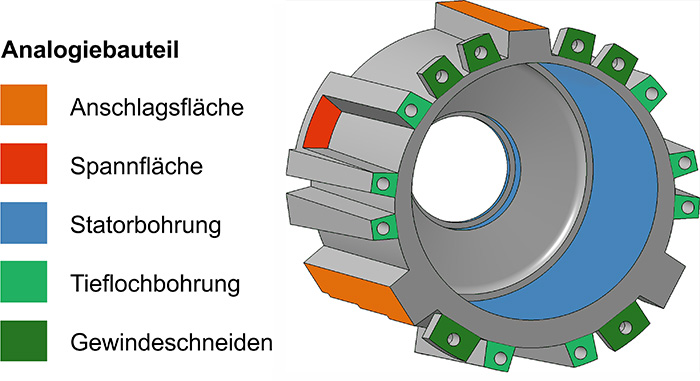
Abb. 2: Analogiebauteil Forschungsprojekt IDaP+ (Quelle: utg der TU München)
Wer soll von den Ergebnissen profitieren und welcher konkrete Nutzen ergibt sich für Unternehmen?
Tim Reeber: Die Abstimmung dieser Prozesse ist bisher nicht erfolgt. Die Elektrifizierung des Antriebsstrangs und die daraus resultierenden Auswirkungen auf die Wertschöpfungskette nehmen deutlich Fahrt auf, insbesondere hinsichtlich der benötigten Prozesse und veränderten Anforderungen an Komponenten. Die kombinierte Betrachtung der Prozesse sowie ein geordneter Austausch von Daten bietet dabei Optimierungspotenziale, um die Produktivität weiter zu erhöhen und gezielte mechanische Eigenschaften zu erzeugen sowie um Hochlaufzeiten zu vermindern und Ausschuss zu vermeiden. Wir werden im Projekt die verschiedenen Akteure in den einzelnen Prozessen für die Möglichkeiten eines Austausches von relevanten Daten sensibilisieren und so neue Geschäftsmodelle und Dienstleistungsmöglichkeiten erschließen.
Profiteure sind demnach Firmen aus dem Bereich der Gieß-, Wärme- und Zerspanprozesse sowie Endanwender wie der Mobilitätssektor oder alle anderen Industriebereiche, in denen dünnwandige Gusskomponenten eingesetzt werden.
Wie sieht das weitere Vorgehen im Forschungsprojekt aus?
Tim Reeber: Wir finalisieren gerade die Analogiebauteilgeometrie und haben erste Simulationen zur Gießbarkeit und Porenfreiheit durchgeführt. Parallel bereiten wir die Simulationen und Experimente in der Wärmebehandlung und in der Zerspanung vor. Wir entwickeln sensorische Werkzeug- und Spannvorrichtungen sowie experimentelle Aufbauten zur Untersuchung des thermomechanischen Zustands während der spanenden Bearbeitung. Basierend auf einer ersten Gusscharge fangen wir an, unsere Simulationsmodelle zu kalibrieren und erste prozessübergreifende Regelungsmethodiken zu entwickeln.
Stimmen aus dem Projektbegleitenden Ausschuss:
Joshua Bissels, Leiter Innovation und Prozessentwicklung Pinter Guss:
Die konsequente Weiterentwicklung hin zu einer digitalen Gießerei wird bei uns im Unternehmen bereits seit einigen Jahren vorangetrieben. Auf Basis einer Betriebsdatenerfassung erfolgt derzeit die Umsetzung der Grundlagen für eine weitreichende Digitalisierung der Prozessdaten. Die Beteiligung am Projektbegleitenden Ausschuss des Projekts IDAP+ zielt darauf ab, sich frühzeitig mit den technologischen Möglichkeiten und Herausforderungen der prozessübergreifenden Verwendung von Produktionsdaten für Qualitätsverbesserung zu befassen. Das Projekt verspricht spannende Einblicke in die Zusammenhänge zwischen Schwankungen in den Prozessen der Gussteilherstellung und der Zerspanung. Im Rahmen des Forschungsprojektes streben wir eine aktive Beteiligung mit unserem Expertenwissen aus beiden Teilen der Produktionskette zur Herstellung fertig zerspanter Bauteile an.
Thomas Rumpf, Konstruktions- und Entwicklungsleitung Hermann Bilz Präzisionswerkzeuge:
Wir sind Hersteller von Präzisionswerkzeugen, die unter anderem auch in Elektromotorengehäusen zur Bearbeitung der großen Statorbohrung als auch der Befestigungsbohrungen eingesetzt werden. Als Mitglied des Projektbegleitenden Ausschusses IDaP+ sind wir an der systematischen Untersuchung der Zerspanungsprozesse und den sich daraus ergebenden Optimierungen unserer Werkzeuglösungen interessiert. Darüber hinaus wollen wir durch die Mitwirkung in diesem Forschungsprojekt unsere bestehenden Kontakte zu den beteiligten Hochschulinstituten pflegen und weiter ausbauen, um Forschungsthemen auch außerhalb dieses Projektes zu besprechen.
Über den Interviewpartner:
Tim Reeber, Mitarbeiter der Gruppe Prozessüberwachung und -regelung am Institut für Werkzeugmaschinen (IfW) der Universität Stuttgart
E-Mail: tim.reeber@ifw.uni-stuttgart.de
Über das Forschungsprojekt:
Das IGF / CORNET-Vorhaben 369 EN der FQS – Forschungsgemeinschaft Qualität e.V. (FQS), August-Schanz-Straße 21A, 60433 Frankfurt am Main wurde im Rahmen des Programms zur Förderung der Industriellen Gemeinschaftsforschung (IGF) vom Bundesministerium für Wirtschaft und Klimaschutz (BMWK) aufgrund eines Beschlusses des Deutschen Bundestages gefördert.
Weitere Informationen finden Sie auf der Website des IfW der Universität Stuttgart »
Kontakt:
ASMET | The Austrian Society for Metallurgy and Materials
Franz-Josef-Straße 18
8700 Leoben, Austria
asmet@asmet.at
Über die FQS:
Die FQS – Forschungsgemeinschaft Qualität e. V. (FQS) unterstützt seit 1989 die anwendungsorientierte Forschung rund um das Thema Qualität in Deutschland. Sie versteht sich selbst als Forschungsbereich der Deutschen Gesellschaft für Qualität e. V. (DGQ) und wird von ihr getragen. Die FQS fördert innovative Forschungsideen über das Instrument der Industriellen Gemeinschaftsforschung (IGF) und des Forschungsnetzwerks CORNET des Bundesministeriums für Wirtschaft und Klimaschutz (BMWK). Ziele der Förderung sind möglichst anwendungsnahe Forschungsideen, die einen unmittelbaren Nutzen für die Wirtschaft, insbesondere für kleine und mittelständische Unternehmen (KMU), erbringen.
Vorstellung der FQS Forschungsgemeinschaft Qualität e.V.
Wer ist die FQS Forschungsgemeinschaft Qualität e.V. und was tut sie? Lernen Sie im Video den Forschungsbereich der DGQ kennen und erfahren Sie von Dr. Christian Kellermann-Langhagen, wissenschaftlicher Geschäftsführer der FQS, wie die FQS arbeitet, welche Themen beforscht werden und wie sich Unternehmen in der FQS beteiligen und von den eingesetzten Förderprogrammen profitieren können.
Kontakt:
FQS – Forschungsgemeinschaft Qualität e. V.
August-Schanz-Straße 21A
60433 Frankfurt am Main
infofqs@dgq.de