Interview: Wie KI-Algorithmen zu einer verbesserten Qualitätskontrolle verhelfen
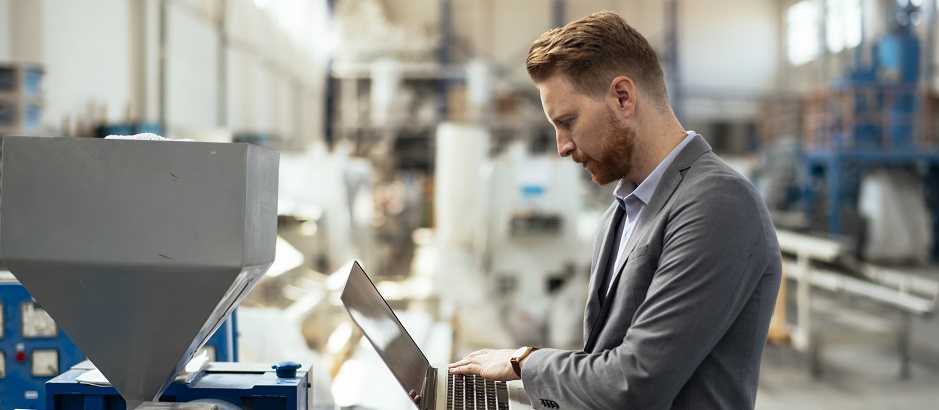
Inwiefern stellt die Automatisierung von Qualitätskontrollen mittels KI-Algorithmen eine nützliche Innovation für Unternehmen dar?
Qualitätskontrollen werden in den meisten Fällen stichprobenbasiert in Form einer Statistischen Prozesskontrolle (SPC) durchgeführt. Gründe hierfür sind hohe manuelle Aufwände bei den Qualitätsprüfungen, nicht existente Daten bzw. bei vorhandenen Daten eine fehlende Data Analytics-Infrastruktur, um eine Qualitätskontrolle auf einer Gesamtpopulation automatisiert durchzuführen.
Stichprobenbasierte Qualitätsprüfungen haben jedoch den Nachteil, dass nur eine kleine Teilmenge von produzierten Bauteilen einer Prüfung unterworfen wird und somit ein ganzheitlicher und vollständiger digitaler Prüfnachweis – beispielsweise für jedes einzelne Bauteil – nicht erbracht werden kann.
In der produzierenden Industrie (v. a. in der Automobilbranche) werden jedoch immer größere Anforderungen an die Nachverfolgbarkeit (Traceability) von Bauteilen gestellt, was im Umkehrschluss perspektivisch in einer digitalen 100%-Prüfung münden wird. Voraussetzung ist eine systematische Erfassung sämtlicher relevanter Prozessdaten (u. a. aus SPS oder spezieller Messtechnik), welche die Grundlage für alle automatisierten und Algorithmen-basierten Prüfrouten sind.
Was sind die Vorteile einer solchen 100%-Qualitätskontrolle?
Die Vorteile sind offensichtlich: KI-Algorithmen erkennen für jedes produzierte Bauteil vermeintliche Qualitätsprobleme, indem Daten des gesamten Produktionsprozesses in die Bewertung mit eingebunden werden. Somit erfolgt die Qualitätsprüfung auf Basis einer Datenmenge, in der deutlich mehr NiO-Teile zu erwarten sind als in einem klassischen stichprobenbasierten Ansatz. Dadurch sinkt automatisch der Anteil der NiO-Teile, was wiederum zu weniger qualitätsbedingten Rückrufen führt und die Kundenzufriedenheit stärkt.
Sollte es dennoch zu Rückrufaktionen kommen, sind Unternehmen deutlich schneller in der Lage, dem Qualitätsproblem auf den Grund zu gehen, da die komplette Datenhistorie in Form von Prozessdaten vorliegt und mit Hilfe von automatisierten Ursache-Wirkungsanalysen durchforstet werden kann. Somit lässt sich das Qualitätsproblem in der Regel auf eine deutlich kleinere Charge eingrenzen. Hohe Rückrufkosten und Imageschäden lassen sich somit vermeiden.
Darüber hinaus können die Ergebnisse der Qualitätsprüfungen in Form eines digitalen Qualitätsfingerabdrucks entlang der gesamten Lieferkette geteilt werden, was zusätzlich Transparenz schafft und die Nachverfolgbarkeit ermöglicht.
Welche konkreten Vorteile ergeben sich hierfür durch die Verwendung von KI?
Die Realisierung einer automatisierten Qualitätskontrolle setzt gewisse Anforderungen an die Dateninfrastruktur voraus, damit sämtliche relevanten Prozessdaten erfasst, gespeichert und verarbeitet werden können. Stehen alle relevanten Prozessdaten zur Verfügung, ergeben sich vielfältige Vorteile und Potenziale.
Vor allem der Einsatz von KI-Methoden in Verbindung mit einer 100%-Prüfung birgt Potenziale, die weit über die Möglichkeiten einer stichprobenbasierten Qualitätsprüfung hinausgehen.
Haben Sie hierfür ein Beispiel?
Natürlich.
Im nachfolgenden Beispiel betrachten wir zwei produzierende Unternehmen A und B, beide Unternehmen stellen vergleichbare Bauteile her, beide Unternehmen haben eine NiO-Quote von 4%.
Nehmen wir an, Unternehmen A produziert 10.000 Bauteile pro Woche, wovon 3% der Bauteile (entspricht 300 Bauteilen) per Zufallsstichprobe „klassisch“ für eine Laborprüfung gezogen werden. Alle geprüften Bauteile werden zerstörend geprüft. Insgesamt finden sich darin 4% NiO-Teile (entspricht 12 Bauteilen). Im Umkehrschluss bedeutet dies aber auch, dass in der gesamten Wochenproduktion mit 4% NiO-Teilen zu rechnen ist (entspricht 10.000 x 0,04 = 400 Bauteilen). Somit werden insgesamt 388 NiO-Teile an den Kunden unerkannt ausgeliefert.
Unternehmen B hat eine KI-gestützte 100%-Prüfung etabliert. Unternehmen B produziert ebenfalls 10.000 Bauteile pro Woche, davon werden 3% der Bauteile (entspricht 300 Bauteilen) nach absteigendem Anomalie-Score selektiert, d. h. die Bauteile mit der höchsten NiO-Wahrscheinlichkeit werden im Labor zerstörend geprüft. In der KI-basierten Selektion befindet sich eine NiO- Quote von 80% (entspricht 240 Bauteilen, d. h. man entdeckt 20x mehr NiO-Bauteile gegenüber Unternehmen A). Bei einer Wochenproduktion mit 4% NiO-Teilen (entspricht 10.000 x 0,04 = 400 Bauteilen) werden somit nur insgesamt 160 NiO-Teile an den Kunden unerkannt ausgeliefert.
Durch weitere Lern-Iterationen wird die Präzision der KI-Modelle immer weiter optimiert, sodass diese Zahl stetig sinken wird. Darüber hinaus kann natürlich jederzeit die Größe der Selektionsmenge KI-gestützt angepasst werden, d. h. dynamisch in Abhängigkeit eines Schwellwertes, der auf den Anomalie-Score angewendet wird.
Wie und womit können Unternehmen eine solche 100%-Prüfung umsetzen?
Bei vielen Unternehmen hat sich Microsoft Excel als das Tool der Wahl für statistische Prozesskontrollen etabliert. Gerade in Bezug auf die Verarbeitung und Analyse großer Datenmengen, deren automatisierte und kontinuierliche Analyse sowie die Verfügbarkeit von KI-Algorithmen stößt Excel jedoch an seine Grenzen. Hier bieten sich beispielsweise Open Source basierte Werkzeuge wie Python an. Auch ohne Programmierkenntnisse lassen sich diese Tools erlernen. Gemeinsam mit der DGQ haben wir ein Training entwickelt, in dem Interessierte die Anwendung von Python in ihrer Qualitätskontrolle Schritt für Schritt erlernen.
Durch den Einsatz von Big Data Analytics Technologien (z.B. Python, PySpark oder Spark) lassen sich bewährte Methoden der statistischen Prozesskontrolle auch auf den gesamten Datenbestand problemlos anwenden. Die bewährten Methoden werden durch die Anwendung auf sämtliche Prozessdaten aufgewertet und durch die Kombination mit KI-Methoden noch wertvoller. Mittels KI-basierten Anomalie-Erkennungs-Algorithmen lässt sich ein kontinuierliches Monitoring im Sinne eines digitalen Qualitätsfingerabdrucks etablieren, um auch kurzzeitig auftretende Prozess-Anomalien jederzeit zu identifizieren und entsprechend behandeln zu können.
Ein digitaler Qualitätsfingerabdruck kann beispielsweise über einen DataMatrix-Code entlang der gesamten Lieferkette geteilt und verfügbar gemacht werden und stellt somit eine wesentliche Komponente im Rahmen zukünftiger Nachverfolgbarkeits- bzw. Traceability-Initiativen dar.
Welche Voraussetzungen z. B. hinsichtlich der Verfügbarkeit oder Qualität von Daten müssen in Unternehmen gegeben sein?
Idealerweise liegen sämtliche relevante Daten bereits vor – ist das nicht der Fall muss in einem ersten Schritt die Bereitschaft da sein, sämtliche relevanten Prozess- und Steuerungsdaten zu erfassen, damit diese für analytische Fragestellungen zur Verfügung gestellt werden können. Diese Daten sollten die notwendige Datenqualität haben und lückenlos sein, damit eine 100%-Prüfung auch tatsächlich darstellbar ist. Darüber hinaus wird eine Dateninfrastruktur benötigt, um die notwendigen Daten auch automatisiert verarbeiten zu können. Last but not least wird ein KI-Werkzeugkasten benötigt, um mit den richtigen Algorithmen die passenden Modelle zu trainieren und zu operationalisieren, damit die Prozesse kontinuierlich und in Echtzeit überwacht werden können.
Über den Interviewpartner:
Stefan Weingärtner ist Gründer und Geschäftsführer der DATATRONiQ GmbH, einem innovativen Machine Learning Lösungsanbieter für das Industrielle Internet der Dinge (IIoT). Darüber hinaus ist er Geschäftsführer der AdvancedAnalytics.Academy GmbH, einem Schulungsanbieter in den Bereichen Data Science, Machine Learning und Künstliche Intelligenz. Mit über 20 Jahren „Data Science Berufserfahrung“ im Consulting- und Applikations-Umfeld zählt er zu den erfahrensten und renommiertesten Experten in dieser Domäne. Er ist als Dozent an verschiedenen Hochschulen tätig, Autor zahlreicher Fachbeiträge zum Thema Machine Learning und Herausgeber der Buchreihe “Information Networking”.