FQS-Forschungsprojekt „AM Analytics“: Frühzeitige Defekterkennung für pulverbettbasierte additive Fertigungsprozesse
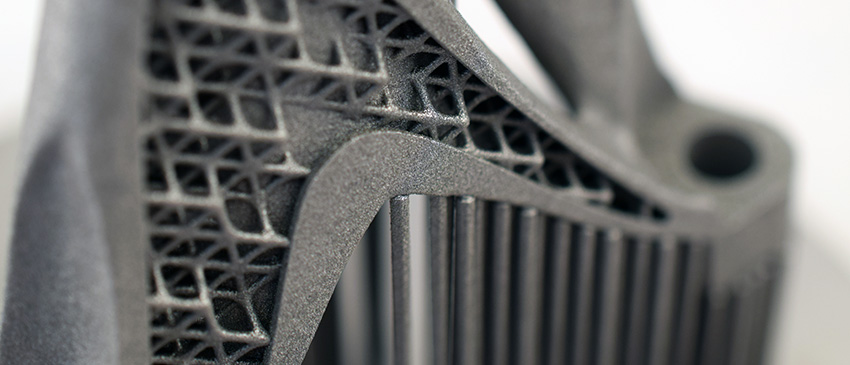
Die Technologie der „Laser Powder Bed Fusion“ (L-PBF-Verfahren) ermöglicht es, Bauteile aus metallischen Werkstoffen additiv zu fertigen. Dabei wird Metallpulver durch einen Laserstrahl selektiv aufgeschmolzen und Bauteile Schicht für Schicht aufgebaut. Diese Form der laser-additiven Fertigung birgt große Potenziale für die industrielle Produktion, da sie beispielsweise die Fertigung individualisierter Bauteile mit unterschiedlichen Geometrien ermöglicht. Eine zentrale Herausforderung für den Einsatz und die weitere Etablierung des Verfahrens in der industriellen Fertigung stellt die qualitätssichere Gestaltung von L-PBF-Prozessen dar.
Im Rahmen des Forschungsprojektes „AM Analytics“ der FQS – Forschungsgemeinschaft Qualität e.V. entwickeln Wissenschaftlerinnen und Wissenschaftler der Fraunhofer-Einrichtung für Additive Produktionstechnologien IAPT und der Helmut-Schmidt-Universität/Universität der Bundeswehr Hamburg eine automatisierte In-situ-Defekterkennung für die pulverbettbasierte additive Fertigung.
Im Interview gibt Philipp Kohlwes, Head of L-PBF am Fraunhofer IAPT, einen Ausblick auf die entstehende Lösung und erklärt, wie Unternehmen von den Forschungsergebnissen profitieren können.
Aus welcher Problemstellung heraus ist das Forschungsprojekt entstanden?
Philipp Kohlwes: Die Qualitätssicherung des L-PBF-Prozesses stellt aufgrund unzureichender Prozesskontrolle und Wiederholbarkeit noch eine Herausforderung für die industrielle Etablierung des Verfahrens dar. Die Folge sind erhöhte Kosten durch Ausschussproduktion. In der Serienfertigung liegt die Ausschussquote durchschnittlich bei 10 – 15 %, bei Produkteinführungen oder Produktionsumstellungen sind es sogar 60 %.
Welche Lösung wird im Forschungsprojekt AM Analytics entwickelt?
Philipp Kohlwes: In unserem Forschungsprojekt wollen wir eine frühzeitige Defekterkennung für den additiven Fertigungsprozess entwickeln, um so die Produktionskosten um mindestens 40 % zu reduzieren. Dazu soll eine In-situ-Defekterkennung entstehen, die in Kombination mit einer intelligenten KI-Datenauswertung kritische Defekte bereits während des additiven Bauprozesses erkennen kann. Mit der Lösung wird eine Detektionswahrscheilichkeit von mehr als 98 % angestrebt.
Wer soll von den Ergebnissen profitieren und welcher konkrete Nutzen ergibt sich für Unternehmen?
Philipp Kohlwes: Schauen wir uns ein Beispiel an: Ein KMU verfügt über fünf additive Fertigungsanlagen mit einer Anlagenauslastung von 64 % im Zweischichtbetrieb. Eine solche Produktion wird durchschnittlich circa 1.800 Baujobs im Jahr durchführen können. Die Fertigungskosten eines einzelnen Baujobs betragen erfahrungsgemäß circa 2.000 Euro. Als typische Ausschussquote werden 12,5 % angenommen.
Berechnen wir für dieses Beispiel die ausschussbedingten Produktionskosten, die durch das Projekt pro Jahr für das KMU eingespart werden können, kommen wir auf einen Betrag von 0,45 Millionen Euro pro Jahr.
Zusätzlich kann durch eine zuverlässige ortsaufgelöste In-situ-Defekterkennung die nachgelagerte Qualitätssicherung effizienter durchgeführt werden. So lassen sich weitere Kosten einsparen. Werden bei dem oben genannten KMU sicherheitskritische Bauteile produziert, so entsprechen die Kosten für die nachgelagerte Qualitätssicherung 70 % der Herstellkosten. Es wird angenommen, dass durch die zuverlässige In-situ-Defekterkennung 50 % der nachgelagerten Qualitätssicherungskosten eingespart werden, da die kritischen Defekte bereits lokalisiert sind. Somit ergibt sich die eine Kostenersparnis von 1,26 Millionen Euro pro Jahr.
Die Rechnung zeigt, dass ein KMU durch frühzeitiges Abbrechen fehlerhafter Baujobs und effizientere nachgelagerte Qualitätssicherung Kosten in Höhe von 1,7 Millionen Euro jährlich einsparen kann.
Wie sieht das weitere Vorgehen im Projekt aus?
Philipp Kohlwes: Zunächst werden die L-PBF Qualitätsanforderungen an die additive Fertigung ermittelt und dokumentiert. Anschließend sollen Experimente mit defektbehafteten Probekörpern durchgeführt werden, die auf industrierelevanten Defekten basieren. In einem weiteren Arbeitspaket werden wir mit Fokus auf die Nutzbarkeit für Algorithmen des maschinellen Lernens eine neuartige Datenstruktur mit kombinierter Sensorik und Prüfdaten entwickeln. Für die entstehende KI-Defektanalytik konzipieren wir im Anschluss mögliche KI-Modelle auf multimodalen Sensordaten und erarbeiten Bewertungskriterien für die Modelle. Auswahl und Hyperparameteroptimierung des KI-Modells wird dann auf Basis der Bewertungskriterien erfolgen. Um Defektergebnisse für die digitale Überlagerung zur Verfügung zu stellen, werden dann Prüfkörper vollständig mit etablierten Messverfahren untersucht. So soll am Ende ein validierter KI-Defektdetektions-Algorithmus zur zuverlässigen Prognose von Defekten basierend auf In-situ-Messdaten der kombinierten Sensortechnologie entstehen.
Stimmen aus dem Projektbegleitenden Ausschuss: Autoflug GmbH
Gemeinsam mit zehn weiteren Industriepartnern ist die Autoflug GmbH als Mitglied des projektbegleitenden Ausschusses „AM Analytics“ an den Forschungsarbeiten beteiligt. Zum Projektstart berichtet Dr. Oliver Burkhardt, Leiter Technologie & Patentmanagement, warum die Autoflug GmbH sich dazu entschieden hat, im Projekt mitzuwirken und zeigt welche Erfahrungen das Unternehmen aus der Praxis einbringen kann.
Dr. Oliver Burkhardt, Autoflug GmbH
Das Forschungsprojekt befasst sich mit der Bauteilqualität in additiven Fertigungsverfahren während des Herstellprozesses sowie mit der frühzeitigen Defekterkennung. Für einen industriellen Endanwender sind Defektraten ein wirtschaftlicher Faktor im Herstellprozess. Andererseits ist es aber auch ein Faktor, der die Zulassung von Serienbauteilen zeitlich verzögert, kostentechnisch unattraktiv oder sogar ganz unmöglich macht. Vorteile der additiven Fertigung können diese wirtschaftlichen und zulassungsrelevanten Nachteile dann nicht mehr kompensieren. Die im Forschungsprojekt entstehende In-situ-Lösung soll dazu beitragen diese Defektraten zu reduzieren.
Mit der Autoflug GmbH haben wir bereits erste Erfahrung in der Entwicklung, Zulassung und Nutzung von additiv gefertigten Bauteilen für den Luftfahrtbereich sammeln können. Dieses Fachwissen zu notwendigen Anforderungen an Bauteile und deren Qualität aus dem Luftfahrtbereich können wir im Rahmen des Forschungsprojektes einbringen, ebenso wie Unterstützung bei der Nachweisführung und die vorhandenen Kontakte zur Zulassungsbehörde.
Über die Interviewpartner:
Philipp Kohlwes, Head of L-PBF, Fraunhofer-Einrichtung für Additive Produktionstechnologien IAPT
Oliver Burkhardt, Dr. Ing. Luft- & Raumfahrt und Patentingenieur, Leiter Technologie & Patentmanagement, Autoflug GmbH
https://www.autoflug.com/de/autoflug-gmbh/
Über das Forschungsprojekt:
Das IGF-Vorhaben 22450 N der FQS – Forschungsgemeinschaft Qualität e. V., August-Schanz-Straße 21A, 60433 Frankfurt am Main wird über die AiF im Rahmen des Programms zur Förderung der Industriellen Gemeinschaftsforschung (IGF) durch das Bundesministerium für Wirtschaft und Klimaschutz (BMWK) aufgrund eines Beschlusses des Deutschen Bundestages gefördert.
Über die FQS
Die FQS – Forschungsgemeinschaft Qualität e. V. (FQS) unterstützt seit 1989 die anwendungsorientierte Forschung rund um das Thema Qualität in Deutschland. Sie versteht sich selbst als Forschungsbereich der Deutschen Gesellschaft für Qualität e. V. (DGQ) und wird von ihr getragen. Die FQS fördert innovative Forschungsideen über das Instrument der Industriellen Gemeinschaftsforschung (IGF) und des Forschungsnetzwerks CORNET des Bundesministeriums für Wirtschaft und Klimaschutz (BMWK). Ziele der Förderung sind möglichst anwendungsnahe Forschungsideen, die einen unmittelbaren Nutzen für die Wirtschaft, insbesondere für kleine und mittelständische Unternehmen (KMU), erbringen.
www.fqs.de
Kontakt:
FQS – Forschungsgemeinschaft Qualität e. V.
August-Schanz-Straße 21A
60433 Frankfurt am Main
infofqs@dgq.de